Safety and Health
Achieving the goal of zero occupational injuries
Nishimatsu Construction’s fiscal 2020 management targets are: continuation of no deaths and no major injuries; a frequency rate of 0.6 or below for injuries requiring four or more days of absence from work (15 or fewer incidents); a frequency rate of 1.0 or below for injuries requiring one or more days of absence from work (25 or fewer incidents); and eight or fewer “big three” accidents, as designated by Nishimatsu Construction (slips/falls; entanglement/catching of head, limbs or clothing in machinery, equipment, vehicles or materials; and flying/falling objects). To achieve these targets, we will focus on the three key management items in our health and safety plan: thoroughly enforce Nishimatsu Rules, establish an autonomous health and safety framework centered on foremen, and firmly establish the seven measures (“Action 7”) for preventing humanerrors.
In working to ensure thorough compliance with Nishimatsu Rules, which incorporate lessons from past incidents and exceed legal requirements, we aim to use the foremen’s association to build ties between foremen, who are the key personnel for on-site health and safety, as we transition from a prime contractor-led system to an autonomous healthand safety framework. Additionally, we will work to firmly establish seven measures for preventing human error: on-site hazard-awareness training (HAT), personal HAT, calling out to fellow workers, the 3-3-3 method (for stringing operations), reporting on employment of older workers and giving them due consideration, raising awareness regarding near misses, and “point and call” safety check routines. Among these seven measures, we will particularly focus on making sure that “point and call” safety check routines become firmly establishedpractices.
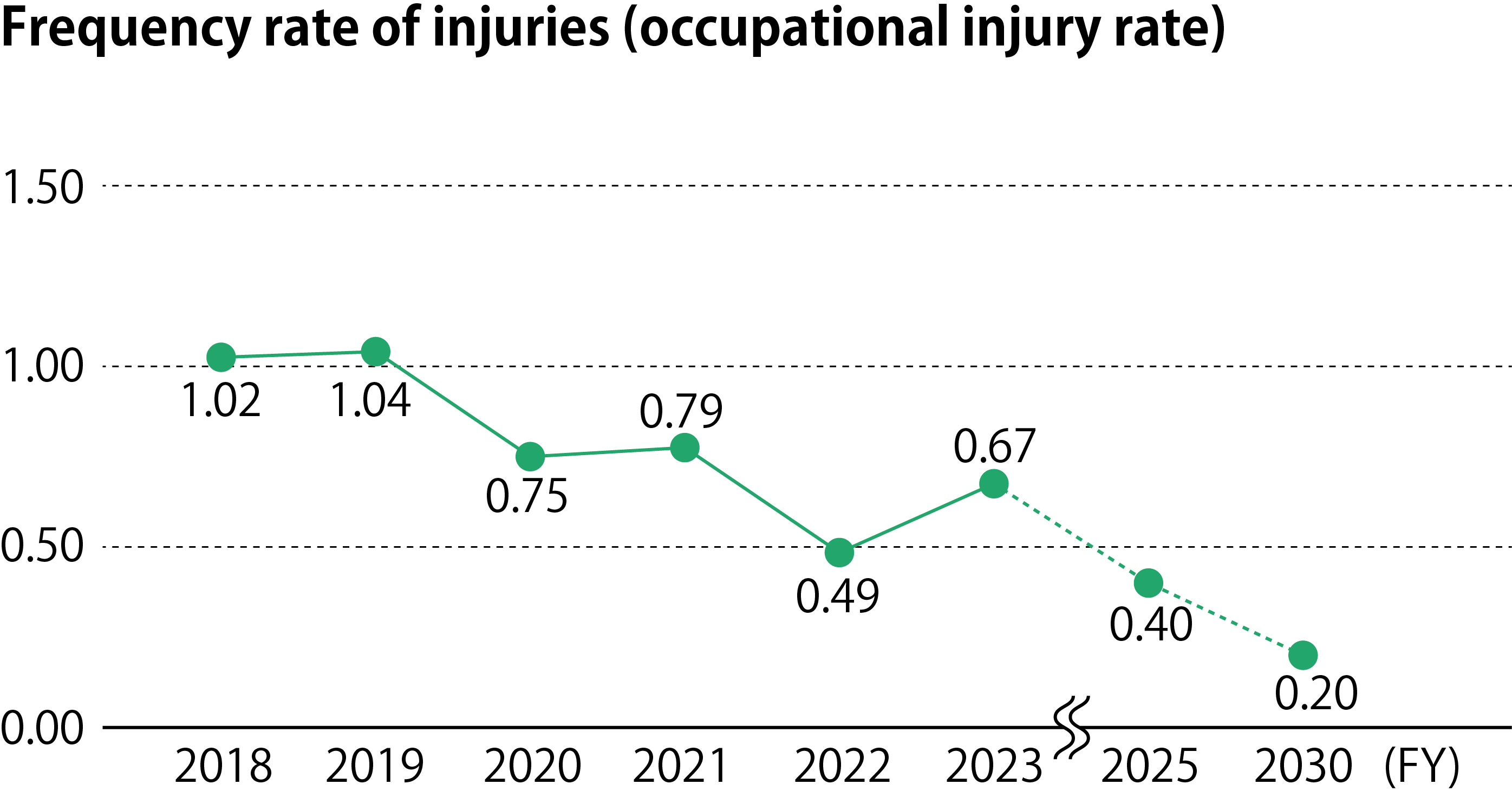
Eliminating long working hours and creating comfortable workplaces
Nishimatsu designated fiscal 2017 as the “First Year of Work Style Innovation,” and has been rolling out initiatives across the Company. In order to solve the particularly pressing problem of long working hours, we are reviewing and implementing a variety of measures, including increasing the efficiency of work processes that contribute to productivity, encouraging the use of ICT devices, and closing construction sites two days a week.
While working to reduce long working hours, we will set KPIs (numerical targets and timelines) so that going forward we can monitor the progress of efforts to promote the use of annual leave and introduce more flexible work styles. Through these initiatives, we are striving to enhance and continue work style innovation.
Concrete Initiatives
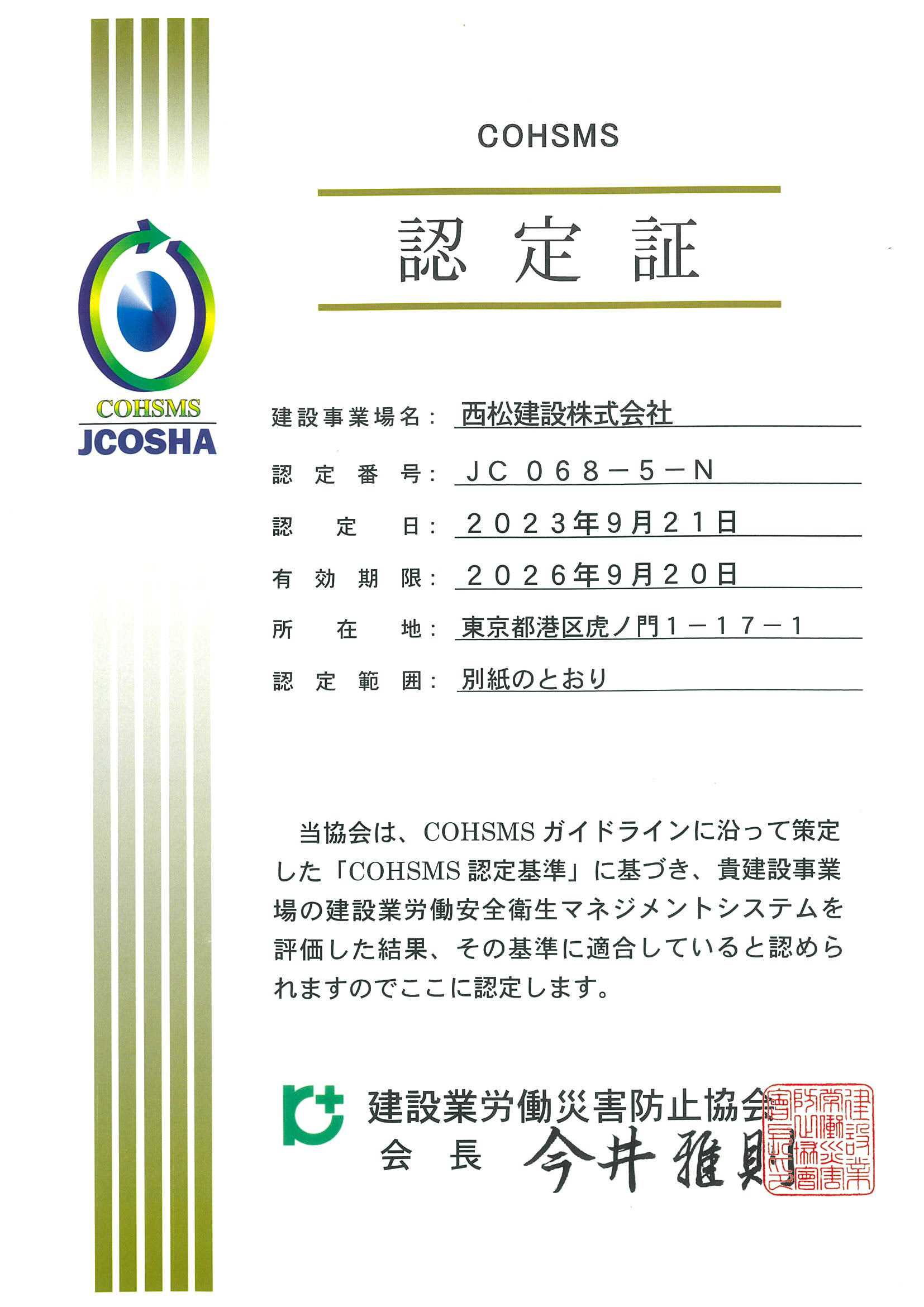
Occupational Health and Safety Management System
Our occupational health and safety management system operates in accordance with Japan’s Construction Occupational Health and Safety Management System (COHSMS). We have transitioned away from the reactive approach of trying to prevent injuries from recurring after they have happened to a safety management approach that removes potential causes of injury in advance through risk assessment. Our aim is to continuously improve health and safety management standards by applying the Plan-Do-Check-Act (PDCA) cycle.
- Major initiatives
-
- 1Eliminating human error to greatly reduce occupational injuries
- 2Improving safe installation practices and enhancing education on health and safety, with efforts centered on foremen
- 3Establishing a standard Company-wide health and safety system
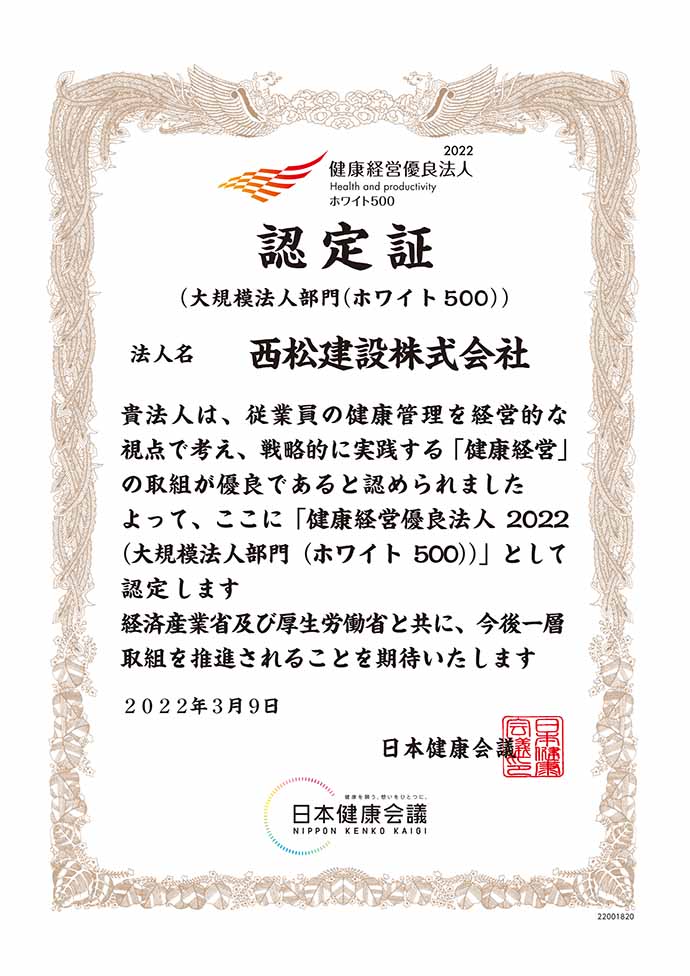
Recognition under the 2022 Certified Health & Productivity Management Outstanding Organizations Recognition Program (White 500) for five consecutive years
The Company was recognized under the 2022 Certified Health & Productivity Management Outstanding Organizations Recognition Program (large enterprise category) (White 500) (*1), jointly sponsored by the Ministry of Economy, Trade and Industry and the Nippon Kenko Kaigi, for the fifth consecutive year on March 2, 2022.
We believe that the physical and mental health of our employees is linked to the sustainable growth of the Company, and we promote the development of a workplace where employees can work in a healthy environment. As part of these efforts, we have made it mandatory since fiscal 2018 for employees aged 30 years or older, who are at increased risk for illness, to take a complete physical examination with the aim of detecting illnesses at an early stage and preventing them from becoming serious. We also began providing paid leave and subsidies to encourage employees to take these examinations, reducing the cost to the individual to nearly zero. We also increased the amount of financial assistance in fiscal 2020 to encourage employees to take optional tests.
Furthermore, we have made it compulsory for employees under the age of 30 to undergo biannual medical examinations with the full cost covered by the Company to educate them to be aware of health management at a younger age.
This certification is in recognition of our efforts to date.
The Company will continue its efforts to raise the awareness of employees on health management and support their efforts to maintain and improve their physical and mental health, thereby creating a workplace where each and every employee can work in a healthy environment.
The Company was also selected as a Health & Productivity Stock (*2) for the construction industry jointly sponsored by the Ministry of Economy, Trade and Industry and the Tokyo Stock Exchange in fiscal 2019.
- *1Certified Health & Productivity Management Outstanding Organizations Recognition Program
This program recognizes organizations, including large enterprises and SMEs, that are practicing outstanding health management (*) based on their efforts to address local health issues and the health promotion initiatives promoted by the Nippon Kenko Kaigi.
The goal is to visualize the outstanding organizations engaged in health management in order to create an environment in which employees, job seekers, related companies, and financial institutions can recognize organizations that consider employee health management from a managerial perspective and work strategically to achieve it. (* “Health management” is a registered trademark of Nonprofit Organization Kenkokeiei.) - *2Health & Productivity Stock
The Ministry of Economy, Trade and Industry and the Tokyo Stock Exchange jointly selected and announced companies that consider employee health management from a managerial perspective and are making strategic efforts to manage their employees’ health as Health & Productivity Stocks. The aim is to promote corporate health management initiatives by introducing companies as attractive to investors who focus on improving corporate value from a long-term perspective.