Industry and Supply Chains
Building fair CSR supply chains
We have been working on a number of concrete activities aimed at achieving this goal, including revitalizing Nishimatsu Construction Subcontractors’ Association (N-NET) and increasing the number of senior foremen. We have achieved positive results, including an improved rate of orders awarded to N-NET members, on a value basis.
Subcontractors in the construction industry are extremely important stakeholders. From a foundation of fair and impartial transactions, we are striving to build win-win relationships through diverse activities.
Concrete Initiatives
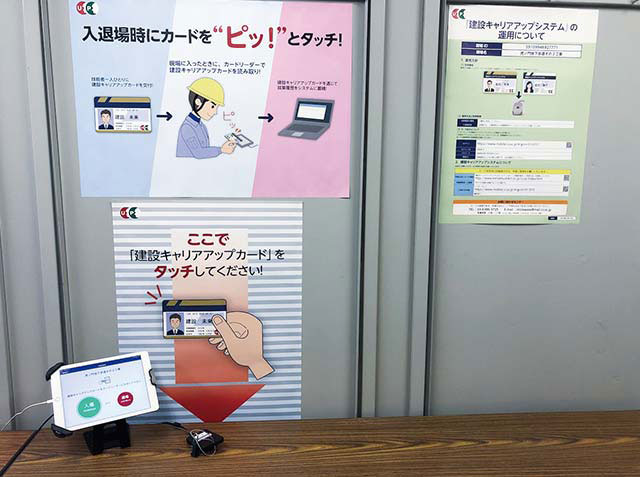
Construction Career Up System
We operate the CCUS for construction work with a contract amount of 50 million yen or more. In fiscal 2019, we held briefing sessions for N-NET member companies, distributed posters and leaflets, and engaged in promoting dissemination. In fiscal 2020, we will work to further informunregistered technicians and to increase their work history. We agree with the purpose of CCUS and will work to improve the problem of a lack of workers and the treatment of construction technicians, which are issues for the entireindustry.
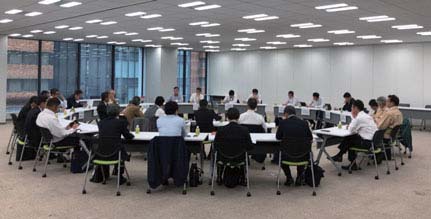
Held the N-NET Growth StrategyConference
Launched in fiscal 2019 with the goals of coexistence and mutual prosperity for N-Net member companies and the Company, the N-Net Growth Strategy Conferenceinvolves collaboration on determining specific solutions and directions to address difficult issues that individual companies cannot solve on theirown.
Title | FY2021 Target |
---|---|
Certified Nishimatsu meisters | 104 |
Certified senior foremen | 356 |
Certified senior foremen of the next generation | 114 |
Certified candidates for Nishimatsu foremen | 92 |
High-caliber technician awardees | 991 |
Employees using the support system to acquire senior technician certification | 87 |
Employees using the senior foremen training program | 173 |
Nishimatsu Meister benefi ts: $00A53,000/day
Senior foremen benefi ts: $00A52,000/day
Senior foremen of the next generation: $00A51,000/day
Candidates for Nishimatsu foremen: $00A5500/day
Strengthening Client and ForemanEducation
Since 2017, we have been focusing on educating clients and foremen, who play an important role in preventing accidents at worksites.
We provide training for all partner companies twice a year under the title “Responsibilities of clients” at safety meetings for regional headquarters and branches, and accident prevention meetings atworksites.
In addition, regarding education to improve foreman skills, we mandate that foremen undergo training within five years from their previoustraining.
Safetymanagementisgraduallychangingfrombeingledby the prime contractor to a framework of safety management carried out by the subcontractors (partner companies) themselves, in cooperation with the primecontractor.
Northern Japan | Kanto Civil Engineering | Kanto Architectural | Western Japan | Kyushu | Total | |
---|---|---|---|---|---|---|
Client education | 422 | 8 | 437 | 609 | 276 | 1,752 |
Skill improvement training for foremen | 203 | 37 | 182 | 275 | 197 | 894 |
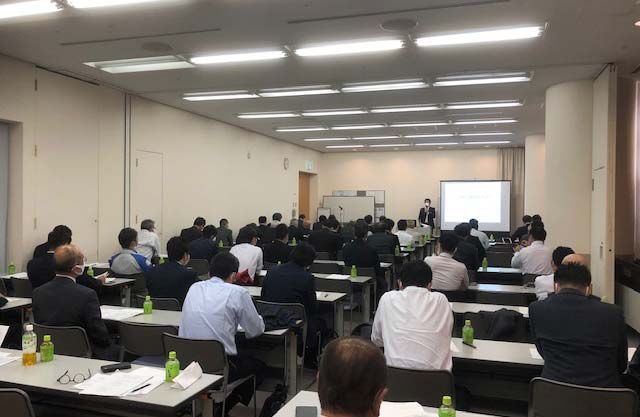
- Clienteducation
- Under the basic philosophy that prime contractors, as well as clients, are the leaders of worksite safety management, we offer seminars twice a year to educate clients on topics they need to understand. COVID-19 made group gatherings challenging in FY2020 and we were only able to accommodate 776 participants (approximately 1/4 the number from the previous fiscal year).
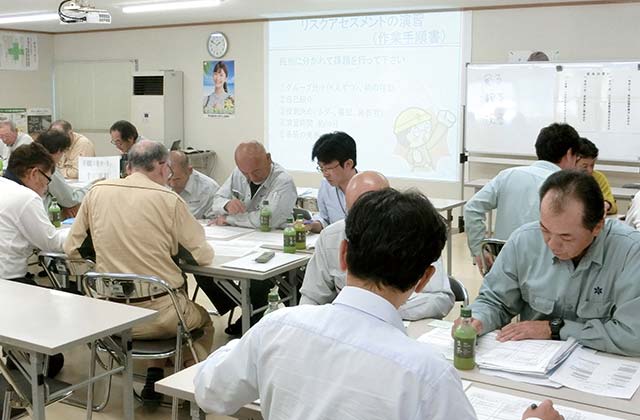
- Skill improvement training forforemen
- Foremen are the key personnel for protecting the safety and health of skilled laborers. Focusing on the foremen’s association, which is composed of these professionals, we mandate attendance at one skill improvement class every five years. The objectives are: worksites with good communication, worksites that are always tidy and organized, and worksites that are meticulous about order. In fiscal 2020, we held 26 classes nationwide and 482 foremen attended.
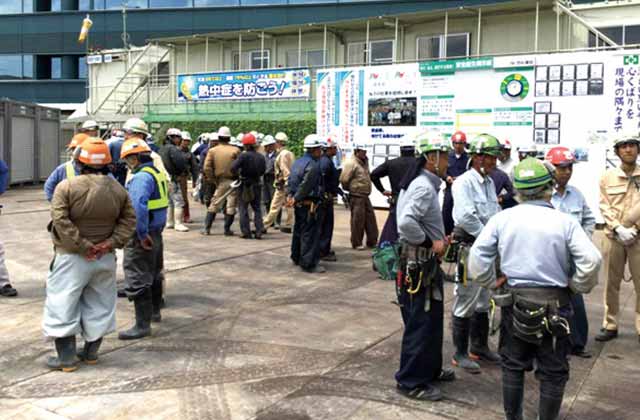
- Checks of physical condition
- As workers age, there is an increasing number of employees with chronic and other health issues on our worksites. If an employee were to lose consciousness on the scaffolding or a staircase, it would be a major issue. Before work starts in the morning and afternoon on worksites, workers gather together by work group, and foremen check the health of those working under them.
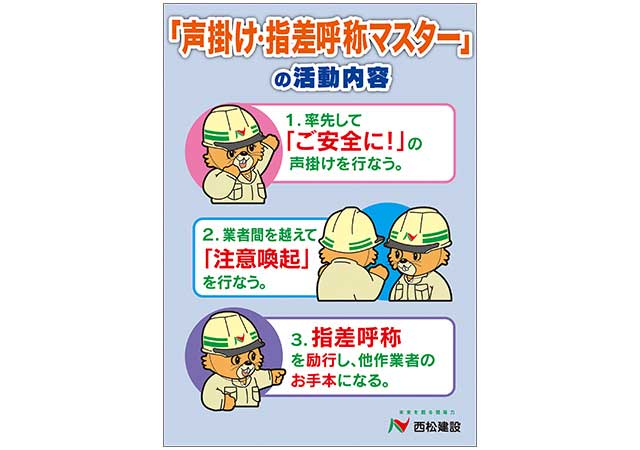
- Initiatives to establish the “point-and-call”routine
- Because there are overwhelmingly more accidents from unsafe practices as opposed to unsafe equipment in recent times, we started seven initiatives five years ago to prevent human errors. To make “pointing & calling” more entrenched, which had been an elusive goal, we rolled out another activity in fiscal 2020. This was appointing “pointing & calling masters” who are central figures for practicing vocal safety and spreading the habit across the entire worksite. The effort has only just got off the ground, though we will continue it going forward to ensure that “pointing and calling” takes place throughout our worksites.