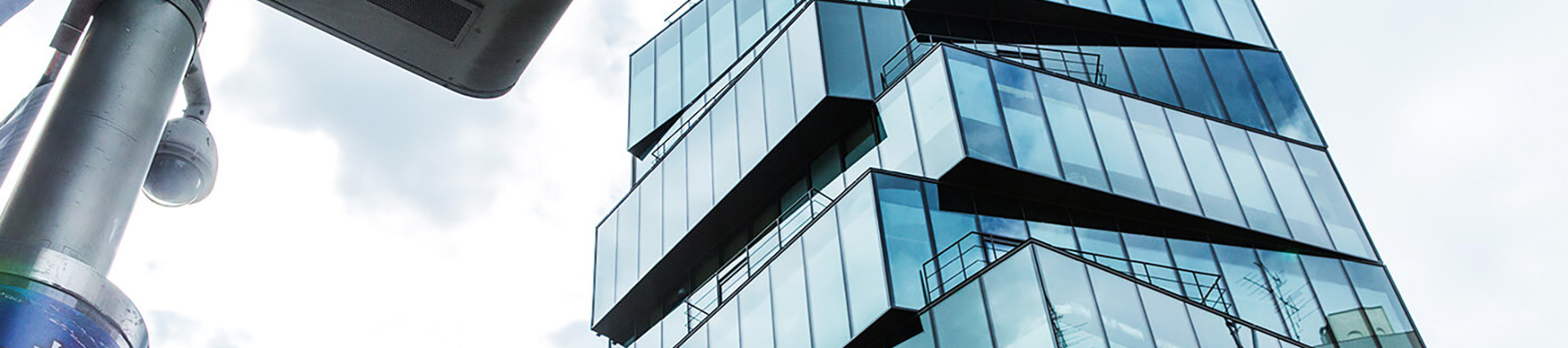
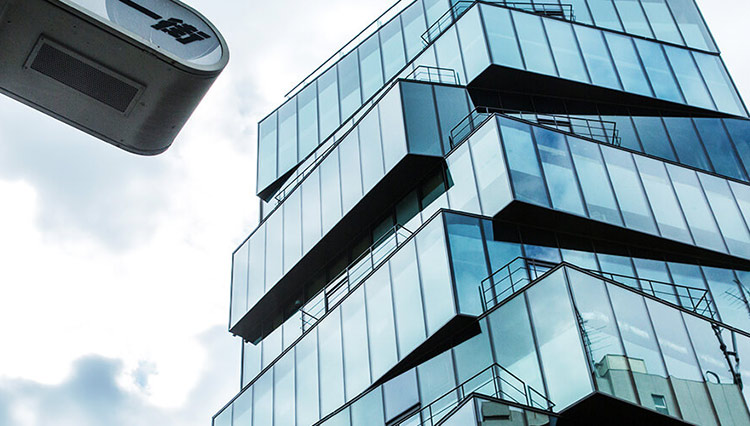
Creating a unique building at Center-gai Street in Shibuya
(Tentative name) New Construction of Hulic Shibuya Inokashira Dori Building
Attracting 50,000 people every day, Udagawa-cho in Shibuya is one of the busiest downtown areas in Japan. Aiming to build a new landmark that will add to the appeal of Shibuya, this project faced many difficult challenges and struggles as well as untold tension. This is the story of a major project that was achieved by overcoming unexpected obstacles.
(Tentative name) New Construction of Hulic Shibuya Inokashira Dori Building
31-1 Udagawa-cho, Shibuya-ku, Tokyo (Residential indication)
Hulic Co., Ltd.
ETHNOS
Retailing stores and restaurants
(2nd basement floor: Wheelchair accessible toilet, bicycle parking, waste storage room, bulky trash collection area
1st floor: Elevator hall (Areas other than these are occupied by tenants.)
Site area: 282.45 m2
Construction area: 231.42 m2
Total floor area: 2,121.19 m2
Top height: 38.637 m
Structure: Steel-frame and steel reinforced concrete structure (1st basement floor: Steel-frame and steel reinforced concrete structure, 2nd basement floor: Reinforced concrete structure )
May 1, 2015 to May 10, 2017
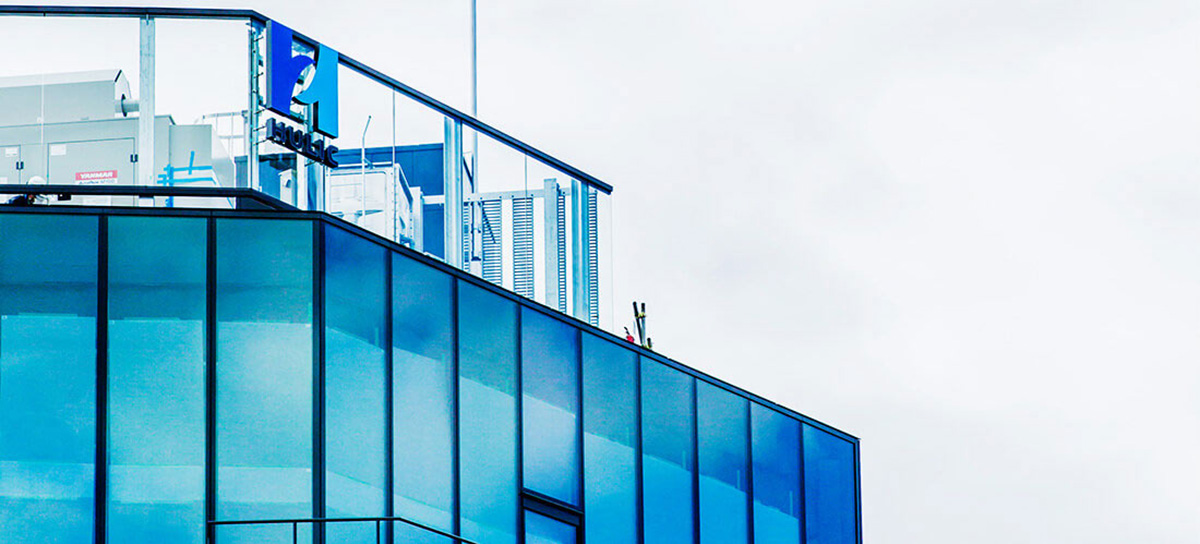
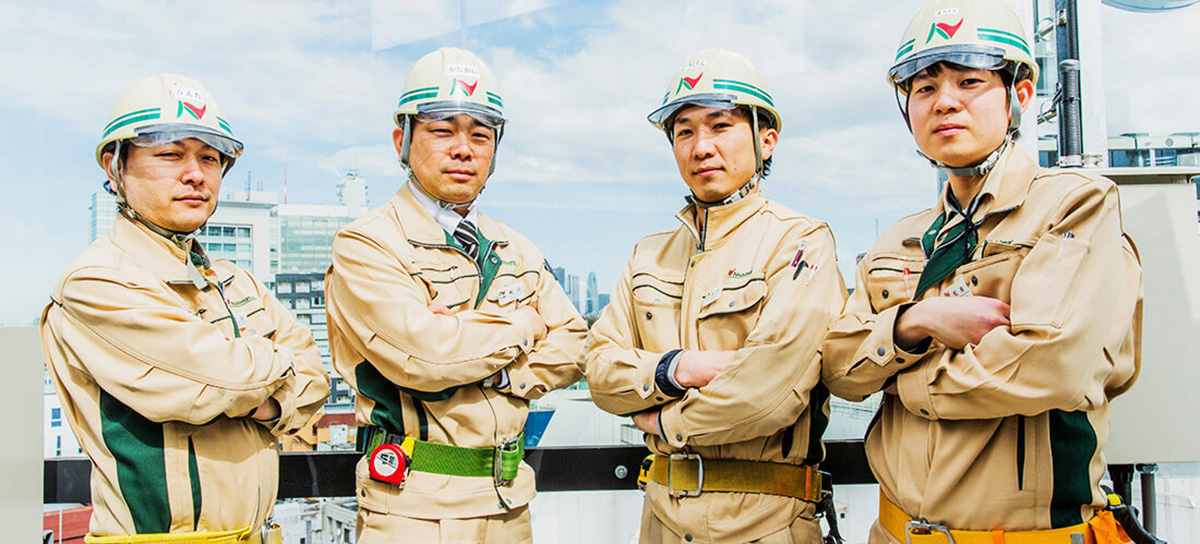
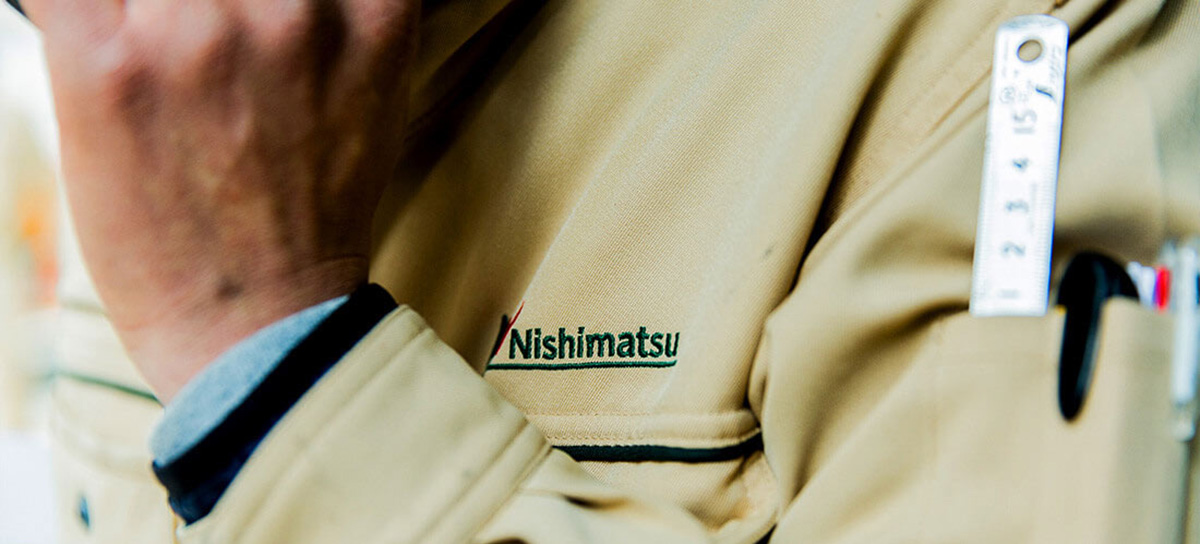
Creating a new landmark at Center-gai Street in Shibuya.
Shaping an unprecedented, new design that was created with true passion.
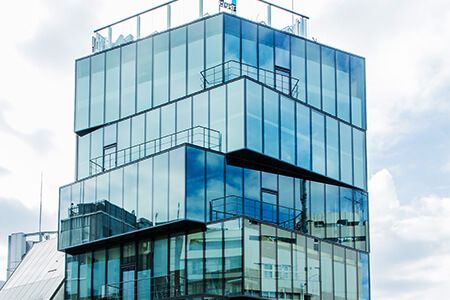
With Center-gai Street and a cluster of commercial buildings for fashion brands and boutiques, Udagawa-cho in Shibuya is one of the busiest downtown areas in Japan.
1A new, notable facility was built in this area, where 50,000 people come and go every day in a constant flow of people and cars, even at night
The building features a unique appearance similar to Jenga, an unprecedented, completely new exterior design symbolizing a sense of diversity and overwhelming existence that attracts attention. The name of this building, which successfully formed a landmark that suits Shibuya as a town for young people as requested by Hulic Co., Ltd., is HULIC & New SHIBUYA. It features 10 aboveground floors and two basement floors. Offering space to tenants engaged in new business and Shibuya’s first tenants, this commercial facility boasts elements that meet the expectations of this town.
During its construction, those who worked at the vibrant construction site faced numerous hardships.
The underground construction work began with difficult challenges and an unexpected obstacle.
Located in an area jam-packed with a variety of buildings, the project site involved various challenges unique to this district, such as narrowness, traffic regulations and the need for close coordination with neighboring commercial facilities. “The underground construction work was filled with hardships,” said Foreman Kajitani, who served as field superintendent. Construction of earth retaining walls was difficult because the site is narrow with high underground water level and an existing underground structure.
Measures included the use of part of the existing underground structure and adoption of the Monroe method for constructing the soil cement pillar line wall, which permits construction work in a limited space with a single heavy machine. Where these methods did not work, the soldier piles and lagging method and the chemical grouting method were applied in combination, thereby securing water-cut-off performance of the earth retaining walls.
However, there was an unexpected obstacle. During the course of the work, it was discovered that the existing underground structure would interfere with the new structure. The new structure was planned to be built on the pressure plate as part of the existing structure. However, because the pressure plate was at a higher elevation than previously indicated, it was impossible to secure the planned floor height without countermeasures.
A proposal to reduce the number of basement floors to one and another proposal to reduce the floor height of the second basement floor were promptly discussed with the client, designer and builder. Top priority was given to securing the planned rentable area, which was strongly requested by the client, and the proposal to reduce the floor height of the second basement floor was adopted.
Mr. Kajitani said, “In the underground construction work, we really experienced hardships, such as using part of the existing structure for the retaining earth and having to change the shape of the new underground structure. However, all related people including those from the design firm applied their wisdom and made adjustments promptly and meticulously, which enabled us to minimize the impact on the construction schedule. It was difficult to transport materials to and from the narrow site while considering the surrounding environment. Things often did not go as planned, which frayed our nerves. However, all of us at the site used our wisdom, held discussions and received support as necessary from a variety of areas, including the Construction Engineering Department of the head office. This was very helpful for overcoming difficulties.”
Because the construction work was difficult, consideration from multiple perspectives was required to solve each challenge. Flexible hands-on capabilities, the extensive experience of Team Nishimatsu and the relationship with third parties—without one of these elements it would have been impossible to complete the project successfully.
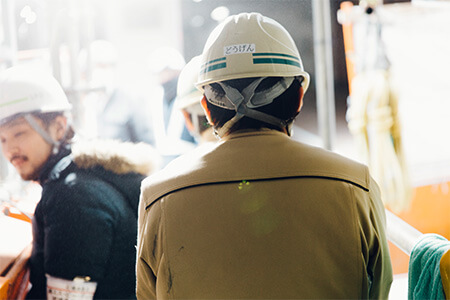
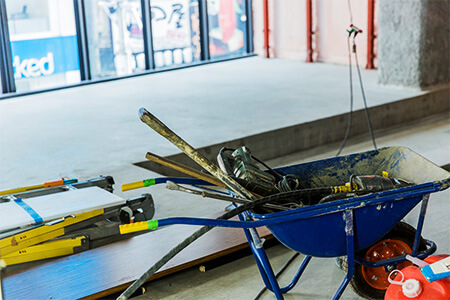
A building without a standard floor.
The site was filled with tension.
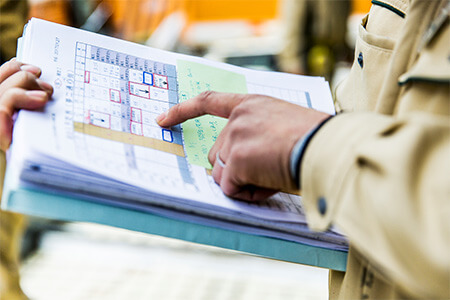
“No two floors had the same shape and appearance.”
This distinctive exterior design, which attracts passersby, reflects the great desire of the client and designer to make the building into a hub for messages in Udagawa-cho, Shibuya. It was also a solution to maximize the use of space.
Naturally, construction work above the ground also included difficult challenges. Due to conditions at the site (including the narrow area and surrounding roads), the crane car (70 tons) that was able to enter the site could hoist up to 9.5-meter steel beams. Because of the building’s structure, which is similar to toy blocks piled randomly, each floor has an overhanging portion. This was the key point that was as puzzling as the underground demolition work. In consideration of the surrounding environment, iron beams were carried to the site and hoisted with the crane at night when the traffic of cars and people was relatively small. Only the assembly of iron beams was carried out at night while coupling, joint welding and final tightening of the beams were conducted in the daytime. Although the assembly work was implemented at night, the site is located in the city center and the work had to be done in a narrow area. This means that maximum attention had to be paid to safety. Otherwise the specified assembly work could not have been completed. Therefore, the site was filled with an indescribable sense of tension.
“Because we were constructing a 10-story building on the narrow site, we had to use reasonably heavy steel beams. We also had to assemble them quickly in the nighttime to avoid safety and noise issues. Due to the condition of the site, we could only work on one side (Yumeji Street). This forced us to remove the front steel joists temporarily to assemble iron beams in the back. We completed this work with tension, fearing that the structure might collapse. Of course, the work was mathematically feasible, but I could not help imagining what would happen if a major earthquake or similar disaster occurred. I spent some sleepless days worrying about the nighttime work,” said Mr. Kajitani. These words tell us all about how much tension people working at the site was feeling.
Overcoming challenges leads to new hands-on capabilities.
An obsession with design and the pursuit of the efficient use of spaces has made HULIC & New SHIBUYA a unique building. To satisfy these desires, even the construction professionals who had extensive experience with working at a variety of sites had to overcome high barriers.
“When I saw the rendering before I was assigned to this project, I couldn’t really imagine how to build it and what challenges had to be overcome. Now it is a fond memory,” said Mr. Kajitani with a smile, looking at the building that would soon be completed. The feelings behind that smile went beyond a sense of achievement, reflecting a sort of pride.
“I had experience with a number of construction sites, including projects on narrow land and construction of high-rise condominium buildings. However, this project felt different. All staff members who worked hard throughout this period discovered something new again and again. Each should be sensing their own development after numerous challenges.”
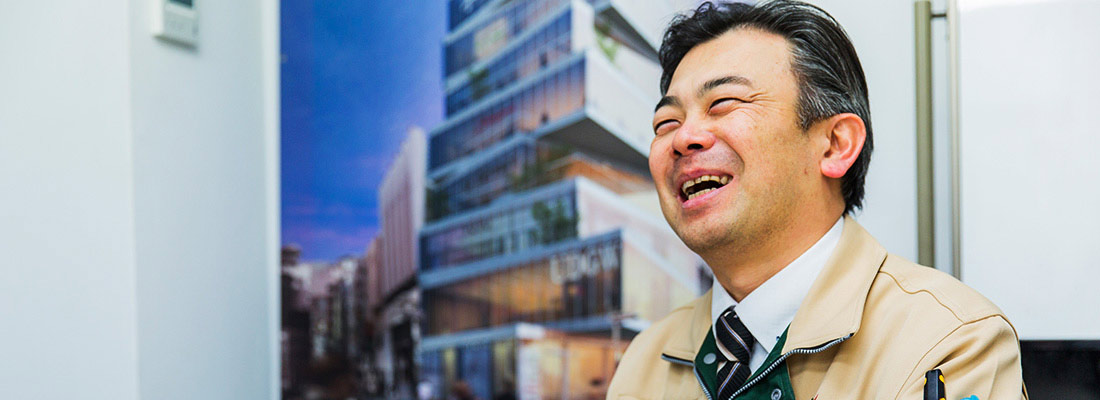
For staff members who were involved in this construction work, the unique building is the fruit of their efforts. They overcame a variety of challenges and what they acquired through this project will be demonstrated as their essential hands-on capabilities in future initiatives.
“I am happy that the experience of this project will allow us to collaborate on a higher level next time.”
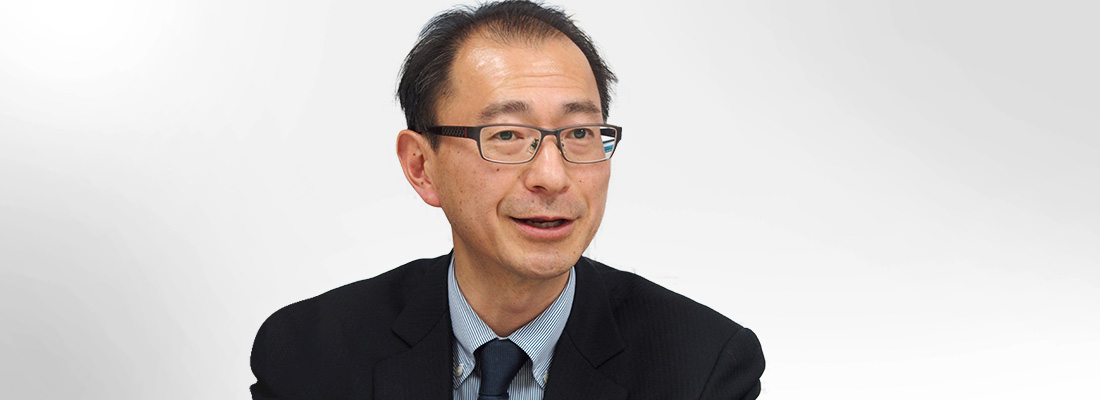
It was a very difficult construction project with tough conditions. Thanks to your efforts, however, the property was completed as a very impressive building. This building is our first self-developed urban commercial facility. It is the new business added to our existing office building business. Therefore, we faced diverse challenges, including many new experiences. Whenever we faced a challenge, we addressed it through dialogues with the three parties.
I think we could not have cultivated the relationship with neighboring facilities without your help. You demonstrated hands-on capabilities in a variety of settings involved in the construction work, including preparations and coordination with neighboring commercial facilities. I am pleased that the experience of this project will allow us to collaborate on a higher level next time.
“I had discussions with you on which construction method to apply to difficult parts. That stands out in my memory. ”
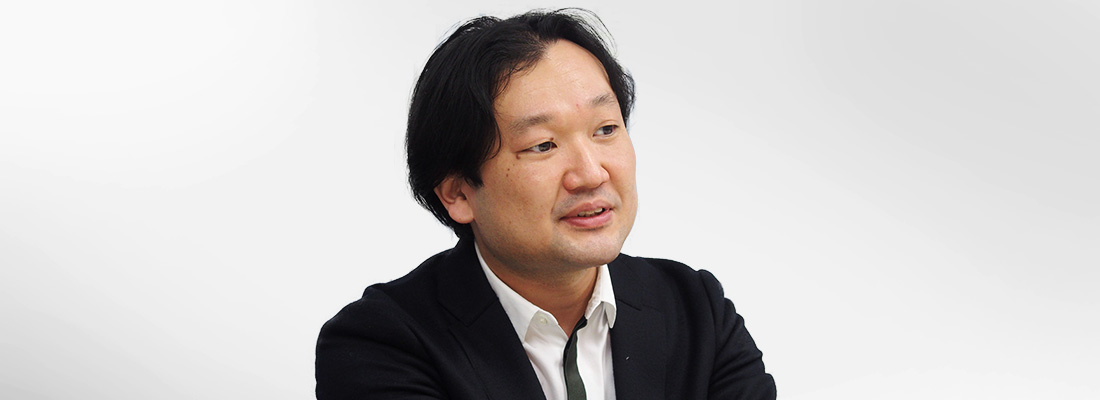
To meet the request from Hulic Co., Ltd. (100% floor-area ratio), it was essential to comply with the setback regulation from road width and fulfill other conditions. Therefore, we decided to design the building by using sky factor*. This is how the building was designed. Of course, we also gave full consideration to its appearance as the information hub of Udagawa-cho, Shibuya, and reflected our thoughts in the design.
We were very particular about not only the appearance of the entire building but also its details, such as overhanging slabs, eaves soffit and parapets. Therefore, I frequently visited the site while the building was being constructed. The most difficult part was the intersection between eaves soffit and the parapets (20-mm clearance). I discussed with you which construction method to apply to those parts. That stands out in my memory.
This and the Omori Building project reminded me that a higher level of collaboration with the three parties enables such an excellent job.
- *Sky factor: Solid angle projection ratio of the sky used in architectural design. Unlike the setback regulation from road width and one from the northern site boundary, sky factor permits judgment based on the ratio between the building and the sky, which is more realistic. It permits the efficient use of space and allows for greater design flexibility. Sky factor was included in the conditions for relaxing the setback regulations under the revised Building Standards Act (2002).